

There are four primary engine simulation commercial packages used in the automotive industry today: Ricardo Wave (RW), Lotus Engine Simulation (LESoft), AVL fire, and GT-Power. Various commercial packages have been developed and are available to solve engineering problems related to design and optimisation of internal combustion engines (ICEs). Once the algorithm has been developed and tested, it may be installed into the ECU. It allows flexible and low cost development of control algorithms without the need of engine bed. In order to develop suitable controls strategies, simulation has been a valuable tool to predict and optimise key parameters in the engine control system. The engine parameters, such as the ignition timing, are then continuously updated according to the feedback of the particular sensor. Other types of sensors, such as lambda sensor, engine temperature sensor, or knock sensor are used on closed loop control configuration. In open loop configuration, the ECU adjusts the engine parameters according to the sensors outputs with the help of look-up tables. Sensors connected to ECU in Figure 1 may be used in open loop strategies, such as air-flow sensor, air temperature sensor, and throttle position sensor. The main component of the electronic control system is the engine control unit (ECU), an electronic device which is connected to the engine sensors and actuators to calculate the best parameters needed to perform efficient combustion, and hence provide cleaner exhaust gas and better engine performance. However, it has to be noted that those requirements can lead to contradictory constrains to be satisfied by the control algorithms. Engines fitted with electronic control provide flexibility to adjust the engine parameters to achieve certain performance. Lately, control engineers in the automotive industry have been challenged with the task of improving fuel consumption and engine performance while simultaneously reducing pollutant emissions. Moreover, those are in reasonable agreement with the reference results while in-house developed package is possible to run simulations with changing speed for engine control purpose. Different numerical experiments have been carried out from which it can be concluded that all packages predict similar profiles of pressure and temperature in the engine cylinder.

These packages are compared with an in-house developed package and with reference results available from the literature. In the present study, two of the commercial packages, Ricardo Wave and Lotus Engine Simulation, have been tested on the capabilities for engine control purposes. Such techniques include variable valve timing, variable ignition timing, variable air to fuel ratio, and variable compression ratio.
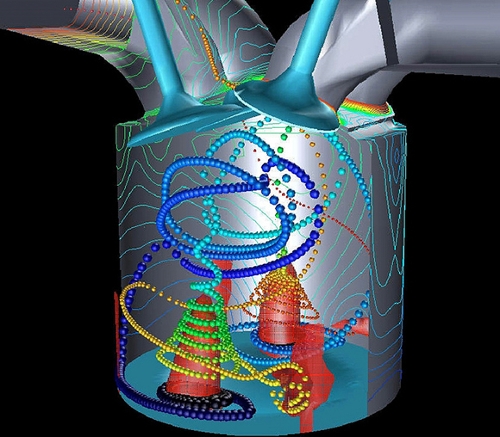
ECU computes the new set of parameters to make fine adjustments to actuators providing better engine performance. Various sensors are installed into the engine, the combustion performance is recorded, and data is sent to engine control unit (ECU). However, engine control involves different operating parameters. These parameters are required for advanced research on fluid flow and heat transfer and development of geometries of engine components. Most commonly used commercial engine simulation packages generate detailed estimation of the combustion and gas flow parameters.
